OTD THROUGH AI
- Home
- OTD THROUGH AI
OTD THROUGH AI
OTD THROUGH AI
The AI system activates AI APS scheduling, offering full order visibility, real-time feedback, and updated delivery timelines. Customers can track orders via the AI app without contacting sales reps
OTD-on time delivery
Jcsportline Group leads the industry by harnessing its proprietary AI management system and digitized factory, seamlessly integrating traditional ERP, PLM, MES, and APS systems into a unified platform infused with AI computation. This revolutionary approach completely resolves the challenges arising from scattered data and inconsistent information, thereby eliminating delays in delivery schedules.
Our system boasts rapid analytical capabilities, providing timely decision support to factory management personnel in efficiently addressing potential bottlenecks across various stages.
Upon customer order placement, our AI system immediately activates AI APS scheduling, ensuring full visualization of orders with real-time anomaly feedback and updated delivery timelines. This empowers customers with comprehensive insights into order progress. Historical data indicates an exceptional order fulfillment rate of 98%, far surpassing the market average of 48%.
This transformative solution embodies our commitment to technological advancement, innovation, and spearheading a technological revolution, setting new standards in efficiency and customer satisfaction.
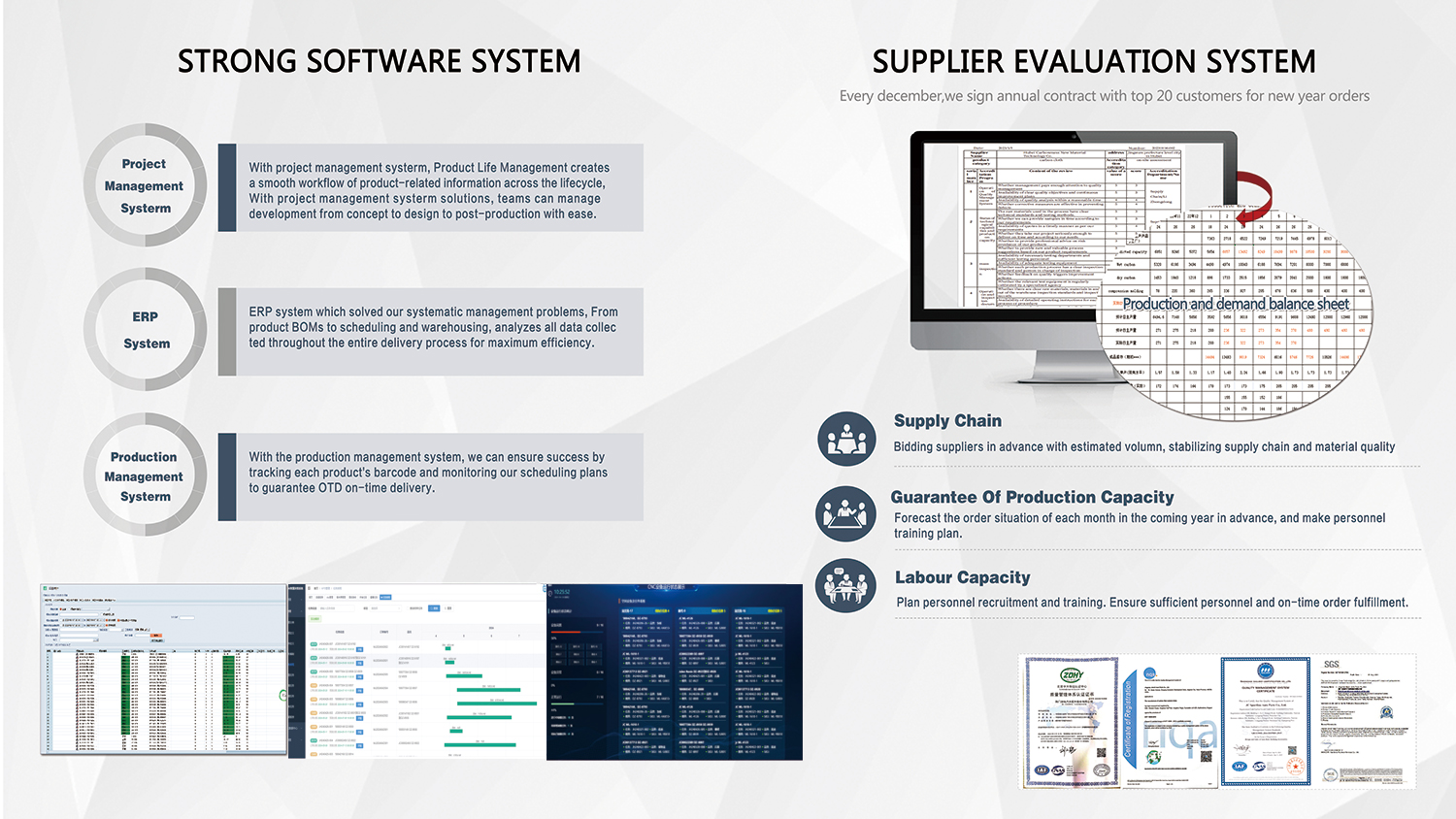
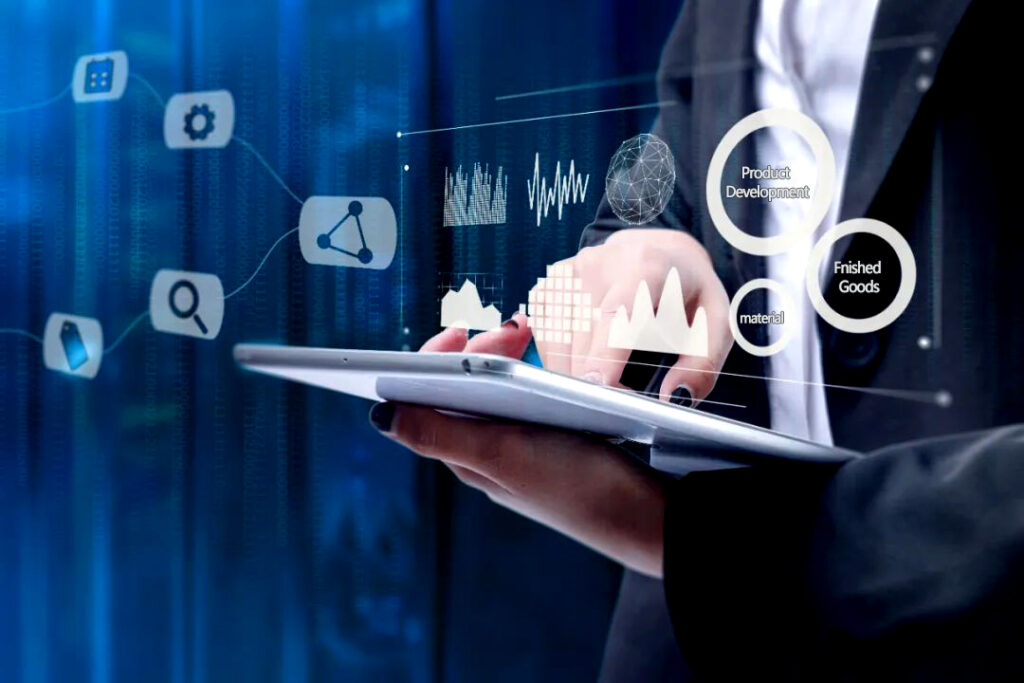
Utilizing AI-powered decision-making, three complementary software management systems encompass product development, material and finished goods control, and end-to-end production process supervision.
- PLM Project Management System: This system ensures the timely delivery of new projects by recording key control points in the product development process.
- ERP (Enterprise Resource Planning): This encompasses the order management system, providing clear and efficient data flow from product Bill of Materials (BOM) to warehouse delivery processes.
- MES (Manufacturing Execution System): This includes the order scheduling system, planning production for each order, and tracking the production process of each product through barcode tracking to ensure on-time delivery.
Supplier Evaluation System
Supplier Evaluation Form – Ensuring Stable Quality:
1. Order Forecasting : Annually in December, the top 20 clients are selected, and the forecast for 80% of the next year’s performance is determined.
2. Organize Supplier: Conferences: Based on order forecasts, a supplier bidding conference is held to assess and score suppliers based on quality and price.
3. Supplier Scoring:
A: Price: Price is a crucial factor, ensuring a competitive advantage for customers in future business.
B: Quality and Performance: Suppliers are evaluated based on customer-specific standards for product quality and performance. For example, in the case of paint, if a customer requires resistance to yellowing for more than 1000 hours, suppliers failing to meet this requirement would be deemed unfit. Similarly, for carbon fiber fabric, resistance to high temperatures up to 120 degrees Celsius is necessary.
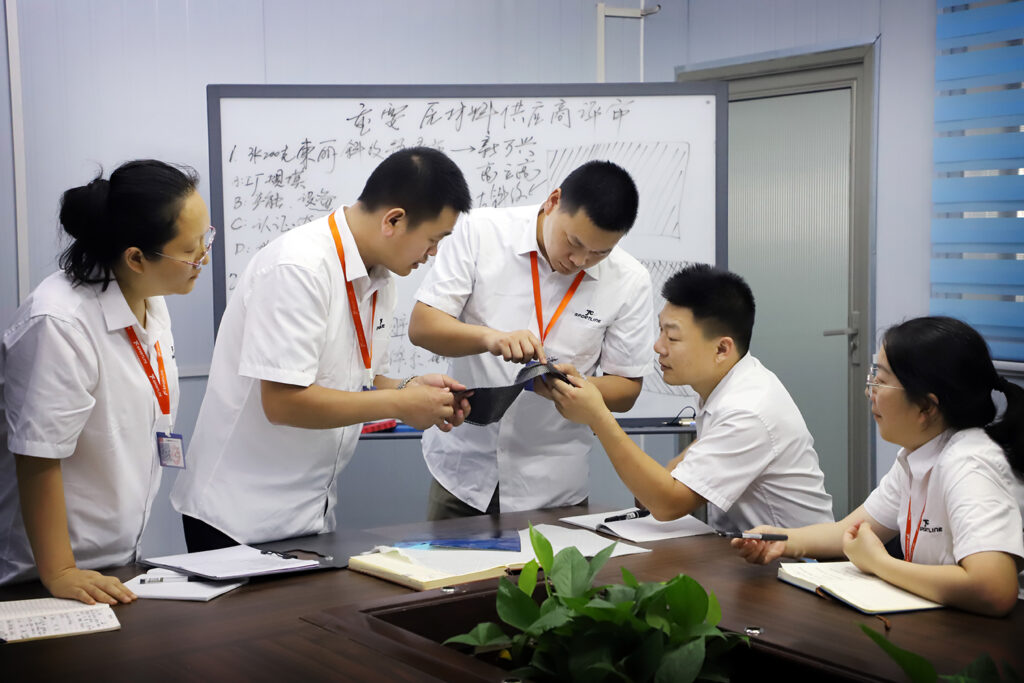
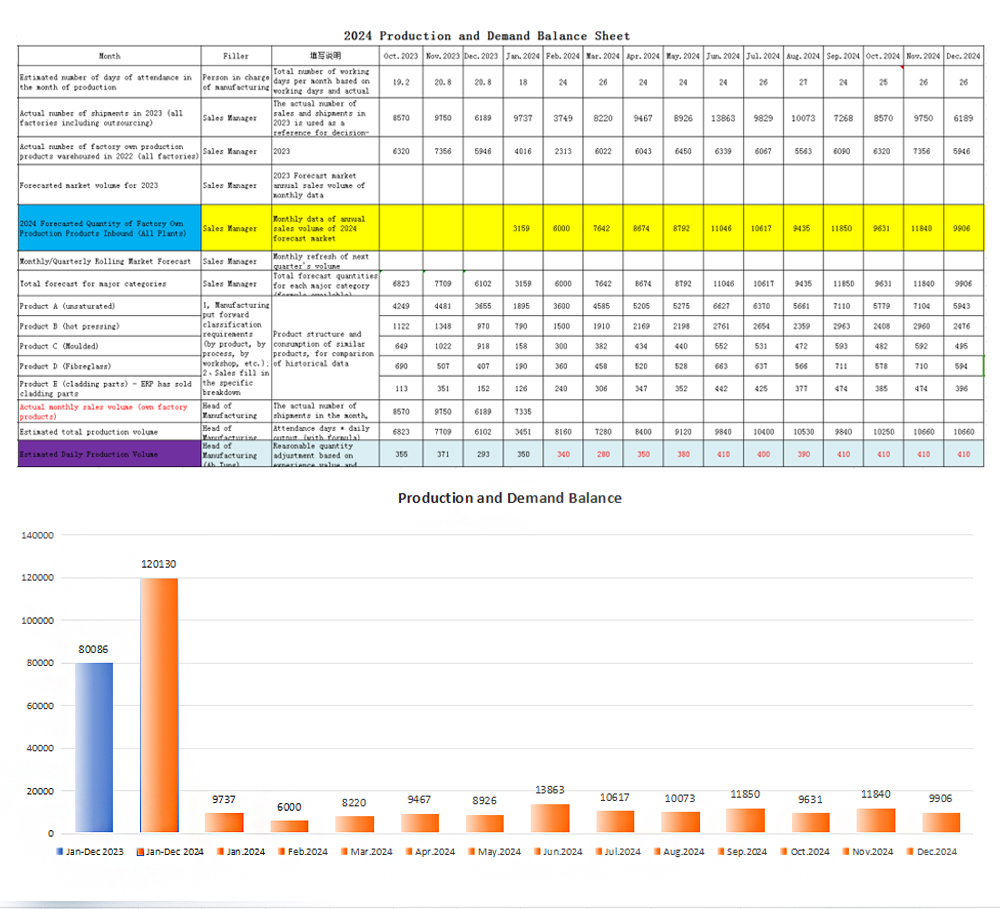
The 2024 production capacity increased by 1.5% compared to 2023.
Production and Demand Balance Sheet - Maintaining Balance between Peaks and Valleys to Ensure On-Time Delivery:
- Order Forecasting: Similar to the supplier evaluation, the top 20 clients are assessed and their performance is forecasted in December.
- Talent Reserves and Worker Training: Based on order forecasts, talent is reserved and workers are trained in advance. This ensures optimization of workforce during both peak and off-peak seasons, guaranteeing on-time delivery of orders.
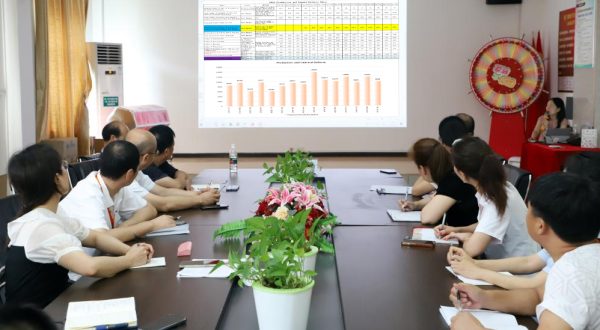
Better quality, efficiency, and applications.
Discover how to apply these advantages to your project