Adhesive bonding of composites
- Home
- Adhesive bonding of composites
Adhesive bonding of composites
Adhesive bonding of composites
Adhesive bonding is crucial in carbon fiber product manufacturing, addressing inherent challenges with traditional joining methods like mechanical fastening. These methods often necessitate drilling holes or puncturing surfaces, which can compromise the integrity of carbon fiber composites by disrupting their matrix and reinforcing fibers. This damage undermines the materials’ exceptional strength-to-weight ratio and structural benefits.
As a solution, adhesive bonding preserves the integrity of carbon fiber composites. Advanced adhesives and tapes now match or exceed the strength requirements of traditional rivets or bolts. Moreover, they offer additional advantages such as sealing joints, preventing galvanic corrosion between different materials, and enhancing the overall aesthetics with a seamless, finished appearance.

- Preparing Raw Materials
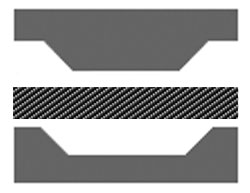
2. Placing Raw Materials

3. Closing the Mold

4. Applying Pressure and Temperature

5. Cooling and Curing

6. Opening the Mold and Retrieving the Product
Adhesive bonding is extensively utilized in carbon fiber production for intake systems, offering significant advantages in both performance and manufacturing efficiency. By eschewing traditional mechanical fasteners, adhesive bonding ensures a seamless integration of components like air intake ducts, manifold covers, and other structural elements.

Aesthetic Appeal
Reduces intake swirl

No Drilling Required
for post-processing


Corrosion Prevention

High Integrity
Through integrated molding
Superior performance and design flexibility
In the realm of carbon fiber product manufacturing, adhesive bonding plays a pivotal role in ensuring both structural integrity and aesthetic appeal, aligning with the demands of modern applications across industries like aerospace, automotive, and sports equipment.
Preservation of Material Integrity
Adhesive bonding maintains material continuity without compromising matrix and reinforcing fibers, unlike traditional mechanical fastening techniques that require drilling.
Strength and Durability
Modern adhesives and tapes offer robust bonds that meet or exceed the strength requirements of traditional mechanical attachments.
Weight Reduction
Adhesive bonding eliminates heavy fasteners, contributing to overall weight reduction, particularly beneficial in aerospace and automotive applications.
Enhanced Design Flexibility
Enables more complex and streamlined designs while maintaining structural integrity due to the absence of fasteners.
Corrosion Prevention
Adhesives can seal joints and prevent galvanic corrosion between dissimilar metals, enhancing the longevity and reliability of the composite structure.
Improved Aesthetics and Cost Efficiency
Results in a cleaner final appearance without visible fasteners, reducing the need for costly finishing work and streamlining manufacturing processes.