Facilities
Compression Molding Process
The compression molding process plays a crucial role in the production of carbon fiber products. Carbon fiber products are highly favored for their lightweight, high strength, and excellent corrosion resistance, with compression molding providing an ideal manufacturing method to achieve these properties.
In the compression molding process, carbon fiber prepreg material is typically placed into a mold and then molded by applying high pressure and temperature. The mold applies pressure of approximately 7 to 20 MPa to ensure the prepreg material flows evenly throughout the mold and fills all the intricate, details and contours. Meanwhile, the heated mold helps cure the resin and ensures the final product meets the required performance and appearance standards.
Prepreg hot pressing
The Prepreg hot pressing process is a critical step in the manufacturing of carbon fiber products, offering a method to achieve their desirable properties such as lightweight, high strength, and excellent corrosion resistance.
In Prepreg hot pressing, carbon fiber pre-preg material, which is already impregnated with resin, is carefully placed into a mold. The mold is then subjected to both high pressure and temperature to shape and cure the material. Typically, pressures ranging from approximately 7 to 20 MPa are applied to ensure uniform distribution of the pre-preg material throughout the mold, effectively filling all intricate details and contours. As the mold is heated during the process, the resin within the pre-preg material softens and flows, allowing it to conform to the mold’s shape. This combination of pressure and heat facilitates the curing process, wherein the resin undergoes chemical reactions to harden and solidify, forming the final carbon fiber product. This ensures that the product meets the required performance and appearance standards.
Vacuum Evacuation Process
The Vacuum Evacuation Process is pivotal in crafting carbon fiber products, renowned for their lightweight, strength, and corrosion resistance. During this process, carbon fiber pre-preg material is carefully positioned within a mold. Subsequently, high pressure and temperature are applied, akin to compression molding. However, the distinguishing feature lies in creating a vacuum environment. This vacuum ensures uniform material distribution throughout the mold, meticulously filling every intricate detail and contour. Simultaneously, the controlled heating within the vacuum facilitates resin curing, guaranteeing that the final product adheres to the stringent performance and appearance standards.
Overlay Process
During the Overlay Process, layers of carbon fiber material are carefully positioned onto a mold surface. Then, under controlled conditions of pressure and temperature, the layers are fused together to form a cohesive structure. The process ensures uniform distribution of the material throughout the mold, effectively filling intricate details and contours.
As the layers are bonded together, the resin cures, facilitated by the heat applied. This ensures the final product meets the stringent performance and appearance standards expected of carbon fiber components.
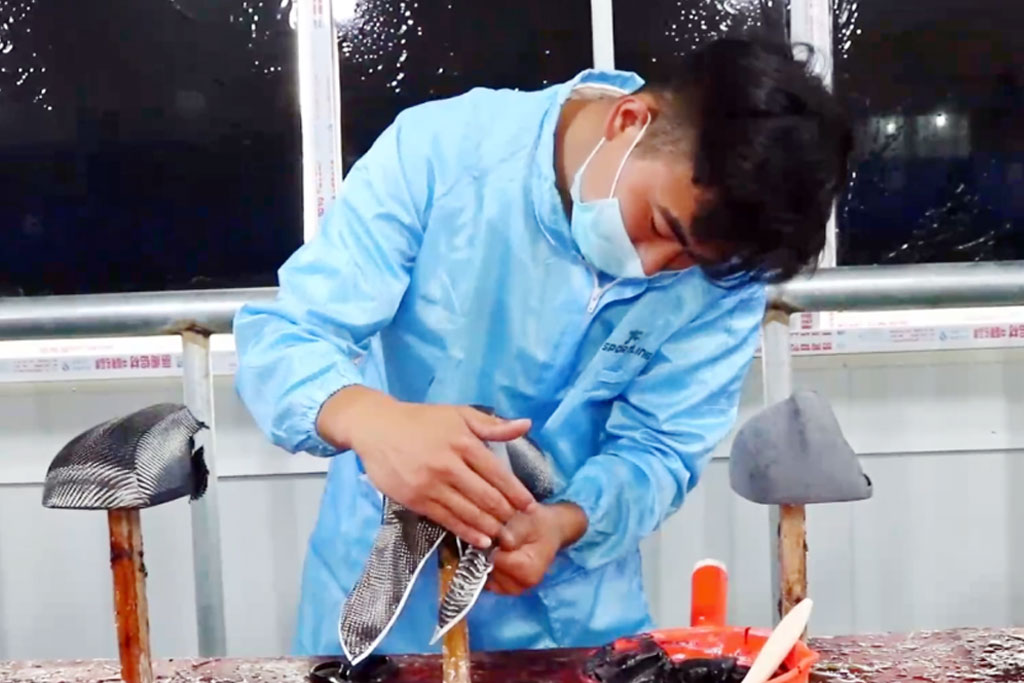
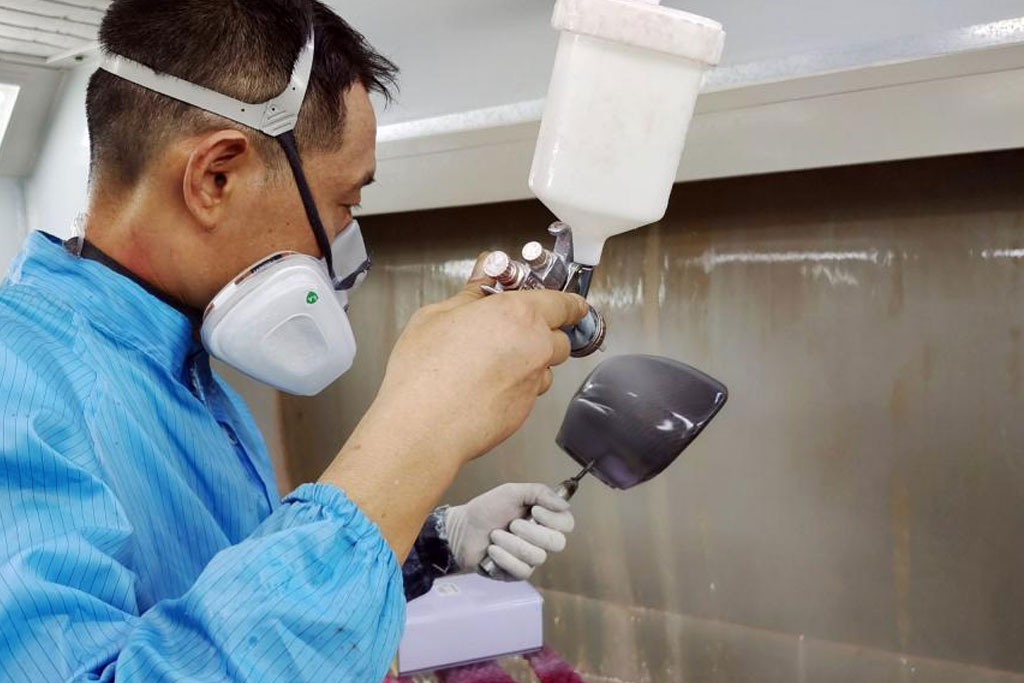
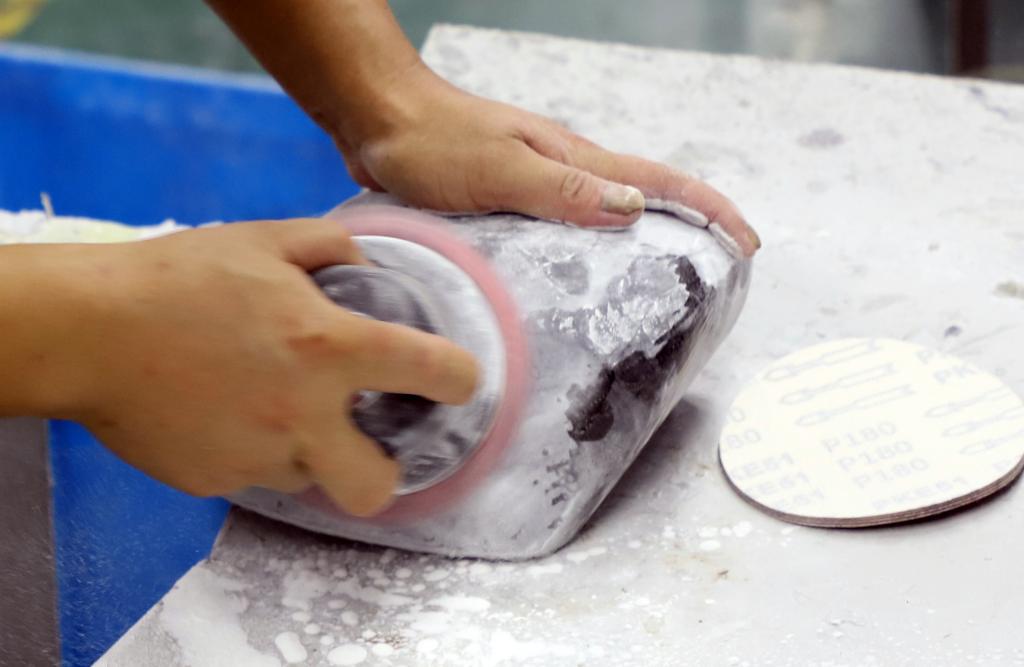
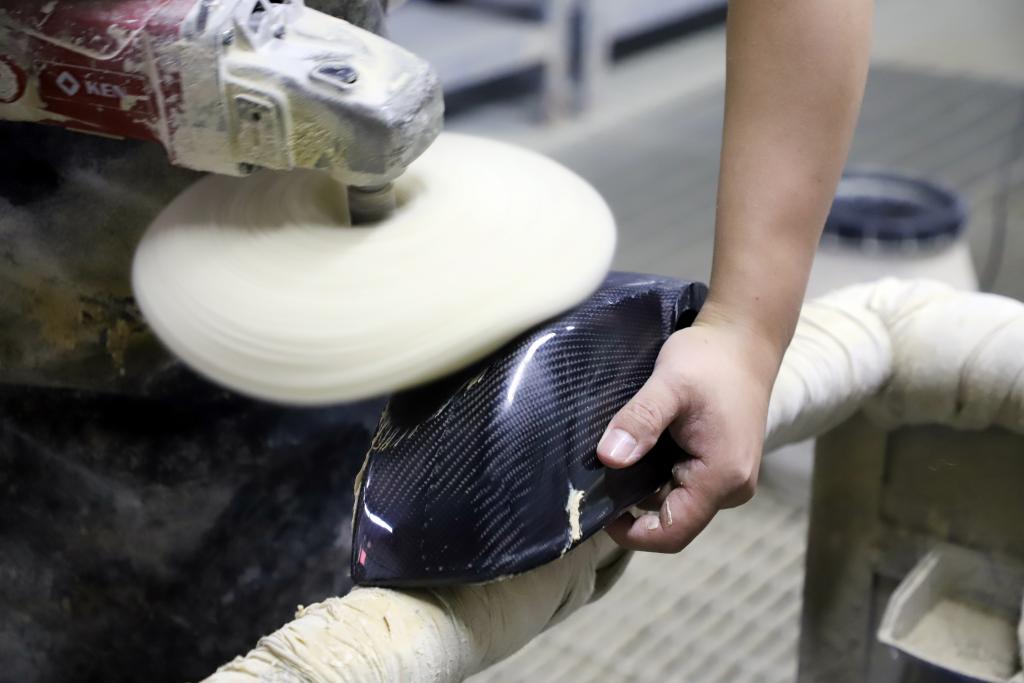
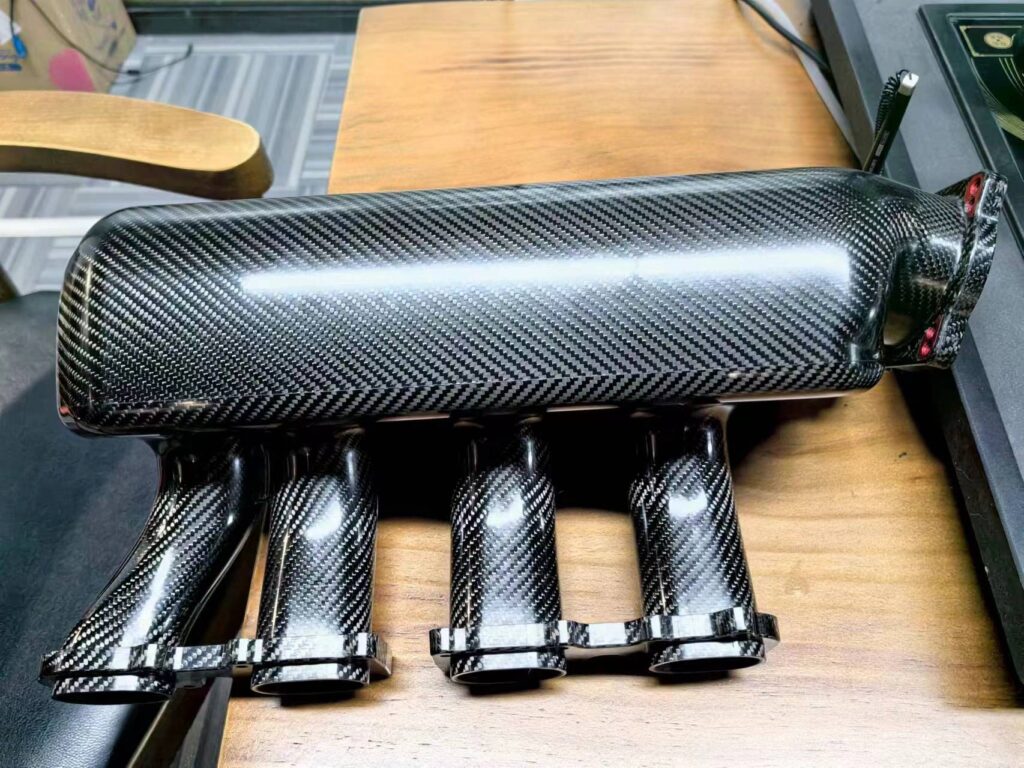
Adhesive Bonding of Composites
Adhesive bonding of composites is a fundamental process in crafting carbon fiber products, renowned for their lightweight, strength, and corrosion resistance. Similar to compression molding, this method plays a pivotal role in achieving these desirable properties.
During adhesive bonding, composite materials are meticulously positioned and bonded together using high-performance adhesives. This process ensures seamless integration of various components, enhancing structural integrity and durability.Under controlled conditions of pressure and temperature, the adhesive effectively bonds the composite layers, ensuring uniform distribution and filling of intricate details. The applied pressure, typically ranging from 7 to 20 MPa, ensures optimal adhesion and consolidation of the composite structure.As the adhesive cures, facilitated by the heat applied, the final product attains the required performance and appearance standards.
Grinding Machine Types
Our factory boasts a wide array of mold options, catering to various requirements such as low-temperature and high-temperature epoxy resin, as well as aluminum and steel molds. With our diverse selection, we ensure to meet the diverse needs of our customers.
Testing equipment
Testing equipment guarantees that carbon fiber products adhere to the necessary standards for strength, durability, and appearance, offering customers benefits such as quality assurance, performance validation, issue diagnosis, cost savings, customer satisfaction, and market competitiveness. By helping customers enhance product quality, reduce costs, and improve market competitiveness and customer satisfaction, testing equipment plays a pivotal role in the production process.
Material Cutting Equipment
Material cutting equipment is crucial for achieving precise and accurate cuts, optimizing material usage, and minimizing waste. This precision is vital for attaining the desired properties of carbon fiber products, including lightweight, high strength, and corrosion resistance. Additionally, carbon fiber cutting equipment enables the fabrication of intricate details and contours necessary for various applications. It offers numerous benefits, including precision cutting, labor cost savings, increased production efficiency, optimized material utilization, enhanced product quality, and flexibility to adapt to various needs. Ultimately, these advantages contribute to improved production efficiency, cost reduction, and enhanced product quality and customer satisfaction.
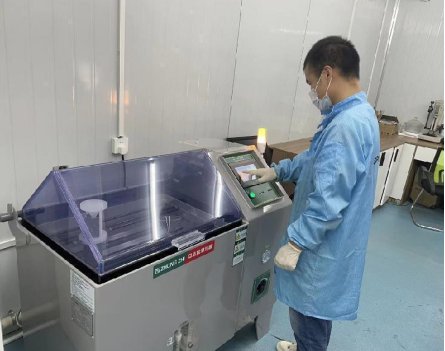
Laboratory
A laboratory serves as a dedicated space equipped with specialized tools and instruments for conducting scientific experiments, analyses, and research. Its primary purpose is to investigate, evaluate, and validate various aspects of products, materials, or processes to ensure compliance with standards, regulations, and quality requirements.
The laboratory provides customers with benefits such as quality assurance, innovation and R&D support, problem-solving capabilities, compliance and safety assurance, time and cost savings, as well as reputation and trust enhancement. These benefits help customers improve product quality, reduce costs, and increase market competitiveness and customer satisfaction.
Material manufacturing & Validation
Material manufacturing and validation aim to ensure that the produced materials meet design specifications, technical standards, and quality requirements. By employing rigorous manufacturing and validation processes, the performance, reliability, and stability of materials are ensured to meet customer needs.