Test Equipment
Constant temperature and humidity test chambers
These chambers are instrumental in evaluating the durability, aging resistance, and corrosion resistance of tested products, ensuring their stability and reliability in various harsh environments.
Carbon fiber materials and composites used in manufacturing undergo rigorous testing to evaluate their performance under different temperature and humidity conditions. These chambers simulate real-world environmental variations to assess the heat resistance, cold resistance, moisture resistance, and overall durability of carbon fiber materials.
During the development phase of carbon fiber products, constant temperature and humidity test chambers are utilized to optimize material compositions and manufacturing processes. By subjecting prototypes to controlled environmental conditions, manufacturers can identify potential weaknesses, refine designs, and enhance product performance and reliability.
Carbon fiber products must meet stringent quality standards to ensure their performance and longevity. Constant temperature and humidity test chambers are employed for quality control purposes, allowing manufacturers to verify product specifications and detect any deviations or defects resulting from environmental stressors.
Carbon fiber products are often subjected to harsh environmental conditions during their lifespan, including temperature fluctuations and exposure to moisture. Constant temperature and humidity test chambers simulate these conditions to assess the long-term durability and reliability of carbon fiber products, helping manufacturers identify areas for improvement and ensure product longevity.
Many industries, such as aerospace and automotive, require carbon fiber products to adhere to specific regulatory standards. Constant temperature and humidity test chambers are used to conduct tests that demonstrate compliance with these standards, ensuring the safety and reliability of products used in critical applications.

Xenon lamp aging test equipment
Xenon lamp aging test equipment is commonly used to simulate natural sunlight exposure and thermal aging environments. It is typically employed to assess the durability and stability of materials under conditions of high temperature, UV irradiation, and humidity.
Xenon lamp aging test equipment finds widespread applications in the manufacturing of carbon fiber products, mainly in the following aspects:
During the development phase of carbon fiber products, it is essential to evaluate the durability and stability of different materials under high temperature, UV exposure, and humid conditions. Xenon lamp aging test equipment can be utilized to conduct aging tests on carbon fiber materials and composites, assessing their performance under real-world usage conditions and guiding material selection and development efforts.
In the production process of carbon fiber products, optimizing process parameters is crucial to improve product quality and performance stability. Xenon lamp aging test equipment can simulate product aging in actual usage environments, assisting manufacturers in adjusting process parameters to enhance product durability and stability.
Effective quality control is paramount for ensuring the performance and lifespan of carbon fiber products. Xenon lamp aging test equipment can be employed to conduct aging tests on carbon fiber products during production, detecting their durability and stability, and ensuring compliance with quality standards and customer requirements.
During product certification and standards compliance processes, a series of aging tests are required to verify product performance and durability. Xenon lamp aging test equipment can be used to perform these tests, providing essential data support for product certification and standards compliance.
Testing Equipment
Start your CF composite project now
Vision Measurement System
Applications
- Precise Measurement
- Surface Feature Detection
- Assembly and Alignment Inspection
- Quality Control in Batch Production
- Non-contact Measurement
Vision Measurement System has significant applications in the manufacturing of carbon fiber products, primarily for precise measurement and inspection of various dimensions and features.
The Vision Measurement System completes measurement and inspection tasks quickly, enhancing production efficiency and inspection speed.
It provides high-precision measurement results, meeting the stringent requirements for dimensions and surface features in carbon fiber manufacturing.
The Vision Measurement System generates detailed measurement data and reports, supporting quality management and decision-making for process optimization.
It is suitable for measuring and analyzing complex structures and fine features of carbon fiber products, aiding in design optimization and manufacturing processes.
Through images and image analysis software, the Vision Measurement System provides visual feedback that is intuitive for operators to understand and analyze product dimensions and features.
CMM Coordinate Measuring Machine
Applications
- Precise Dimensional Measurement
- Shape and Position Detection
- Quality Control
- Reverse Engineering
- Mold Inspection
Benefits
- High Precision and Repeatability
- Increased Production Efficiency
- Reduced Scrap Rates
- Support for Complex Structures
- Data Recording and Analysis
- Improved Customer Satisfaction
Tensile Testing Machine
A tensile testing machine is designed to measure the mechanical properties of materials and products under tensile, compression, bending, and other forces. It applies controlled forces and measures the deformation and failure of materials under different conditions, evaluating key characteristics such as strength, hardness, and durability.
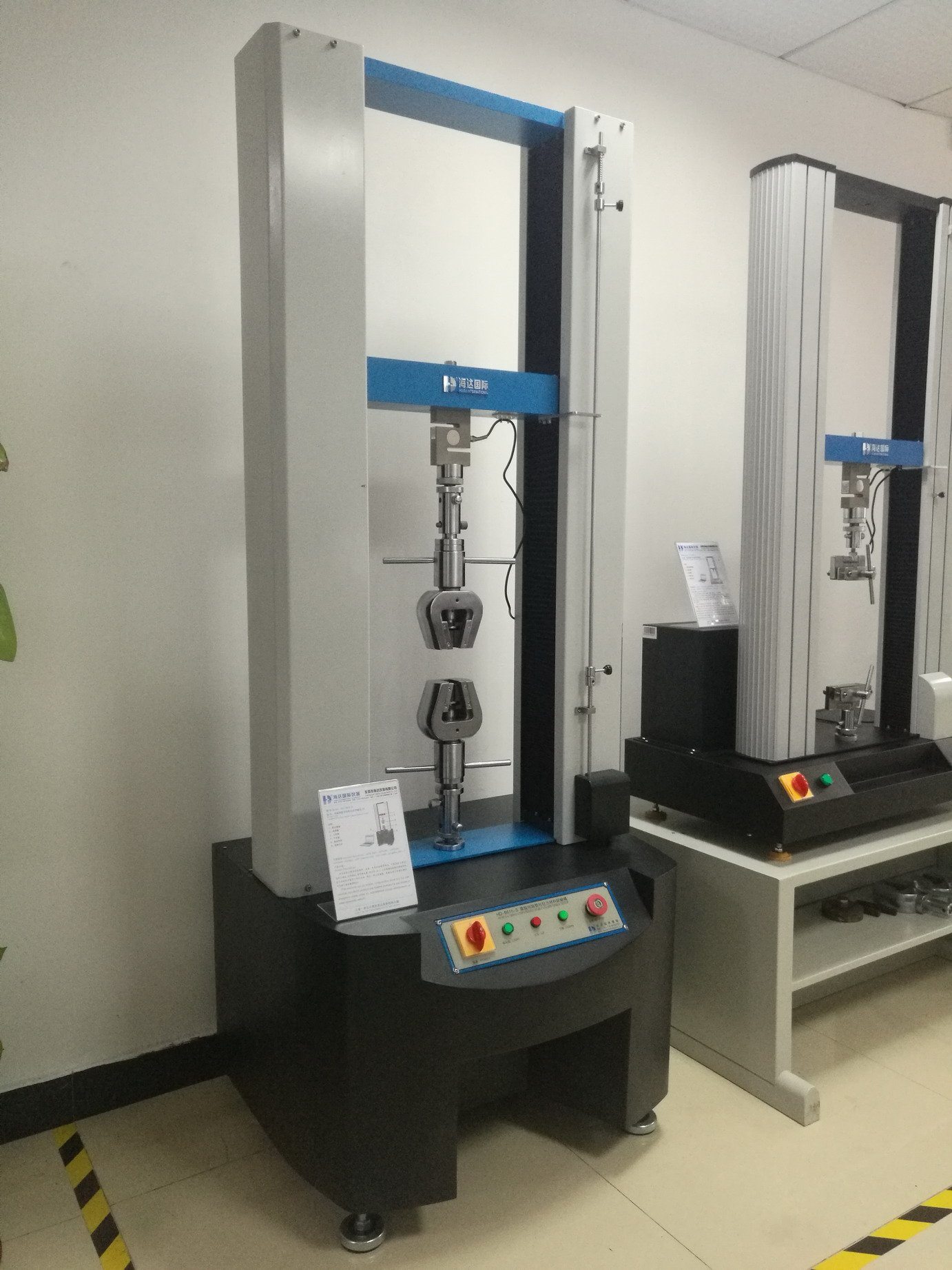
During the development of carbon fiber composites, the tensile testing machine assesses the tensile, compression, and bending properties under different material formulations and processing techniques. Engineers use this data to precisely understand material strength, stiffness, and deformation behavior, optimizing material formulations and processes to enhance overall product performance.
Throughout production, the tensile testing machine ensures quality control and validation of carbon fiber products. Each batch undergoes tensile testing to verify compliance with strength and durability standards, ensuring consistency and reliability in product quality.
Based on data and analysis from tensile testing, manufacturers can iteratively improve and optimize product designs. For instance, in automotive and aerospace applications, understanding the performance of carbon fiber composites under different stress conditions enables the design of lighter and stronger components and structures, enhancing overall performance and safety.
Tensile testing provides objective data on the strength and durability of carbon fiber products, enhancing customer trust and confidence. High-quality test results also help establish a positive brand image and increase market competitiveness.
By early detection of design or material issues through precise testing, manufacturers can reduce costs associated with research failures or production defects. Furthermore, optimizing product design and processes reduces resource consumption, achieving cost efficiency and sustainable development.


A salt spray test chamber is a specialized equipment used to simulate and evaluate the corrosion resistance of materials and products exposed to salt-laden environments. It creates a controlled environment where a saline solution is atomized into a mist, which is then sprayed onto the test specimens.
Salt Spray Test Chamber
Applications and Benefits
During the development phase, the salt spray test chamber evaluates the corrosion resistance of different carbon fiber composites and coatings. This helps engineers and researchers select the most suitable materials and coatings that can withstand harsh environmental conditions, ensuring long-term durability and reliability of the products.
Throughout the manufacturing process, the salt spray test chamber plays a pivotal role in quality control and assurance. It allows manufacturers to verify that carbon fiber products meet corrosion resistance standards specified in design requirements and industry regulations. This ensures consistent product quality and reliability.
Prior to market launch, carbon fiber products must undergo various certifications and approvals. The results from the salt spray test chamber provide crucial data to demonstrate compliance with international standards and regulations, facilitating smooth certification processes and regulatory approvals
The salt spray test chamber enables manufacturers to validate the performance of carbon fiber products in simulated corrosive environments. This includes assessing the effectiveness of protective coatings and surface treatments in preventing corrosion, thereby enhancing product performance and longevity.
By identifying potential weaknesses or vulnerabilities early in the product development cycle through salt spray testing, manufacturers can make informed decisions to optimize designs and mitigate risks associated with corrosion-related failures. This proactive approach reduces overall production costs and enhances product reliability
Versatile Mold Solutions Tailored to Your Needs for Project Success
The use of these advanced testing instruments by JCSPORTLINE translates into significant benefits for customers. Enhanced product quality, safety, optimized performance, compliance with industry standards, cost efficiency, innovation, and increased customer satisfaction are all direct results of these rigorous testing and monitoring processes. By ensuring that every product meets the highest standards, JCSPORTLINE reinforces its commitment to delivering exceptional value and reliability to its customers.
Enhanced Product Quality
Ensures the mechanical strength and durability of carbon fiber products, guaranteeing that customers receive robust and reliable components.
Maintains consistent and high-quality surface finishes, enhancing the aesthetic appeal of the products.
Safety and Reliability
Provides a safe environment for handling hazardous materials during production, ensuring that the products are manufactured under stringent safety protocols.
Verifies the corrosion resistance of carbon fiber products, ensuring their longevity and reliability even in harsh environmental conditions.
Compliance with Standards
Evaluates the adhesion of coatings, ensuring the products meet industry standards for durability and finish.
Provides accurate pressure measurements during production, ensuring compliance with manufacturing specifications and standards.
Cost Efficiency and Resource Optimization
Helps in optimizing energy usage and reducing production costs by monitoring energy consumption and identifying areas for improvement.
Reduces processing times and increases efficiency, leading to cost savings that can be passed on to customers.
Optimized Performance
Ensures precise curing and drying processes, leading to optimal performance characteristics of the final carbon fiber products.
Monitors and controls various production parameters in real-time, ensuring consistent quality and performance of the products.
Innovation and Customization
Supports research and development efforts, allowing JCSPORTLINE to innovate and customize products to meet specific customer needs and preferences..
Enables the development of products with superior corrosion resistance, tailored for specific applications such as automotive and marine industries.